What’s Next for Metal Manufacturing – And Are You Ready?
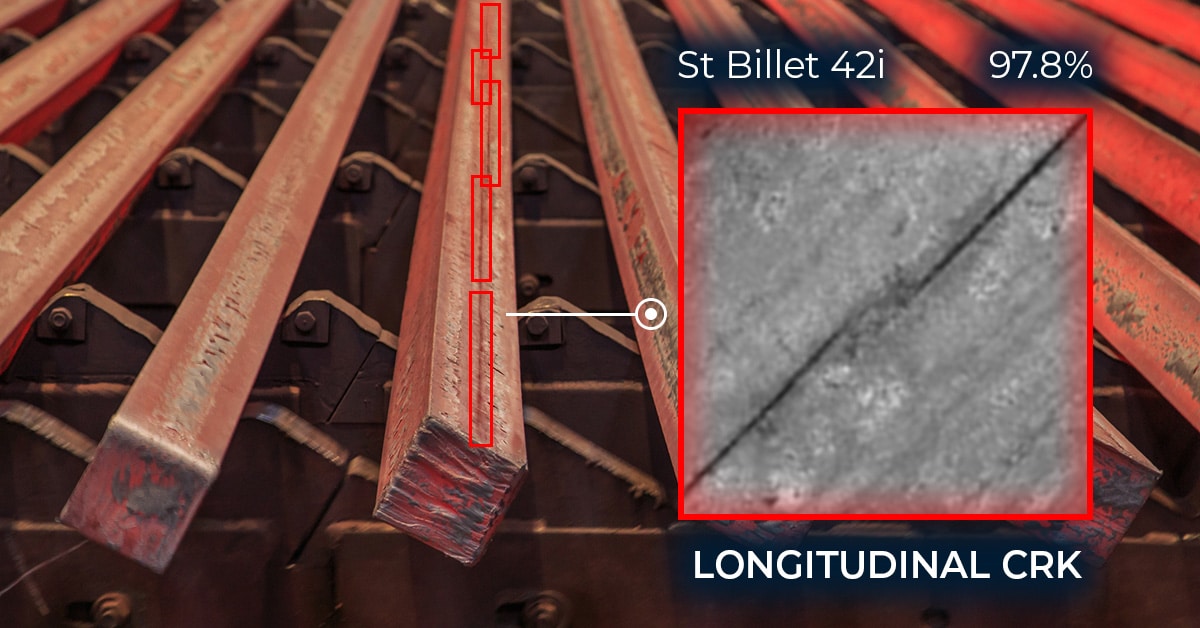
Matroid | June 18th, 2025
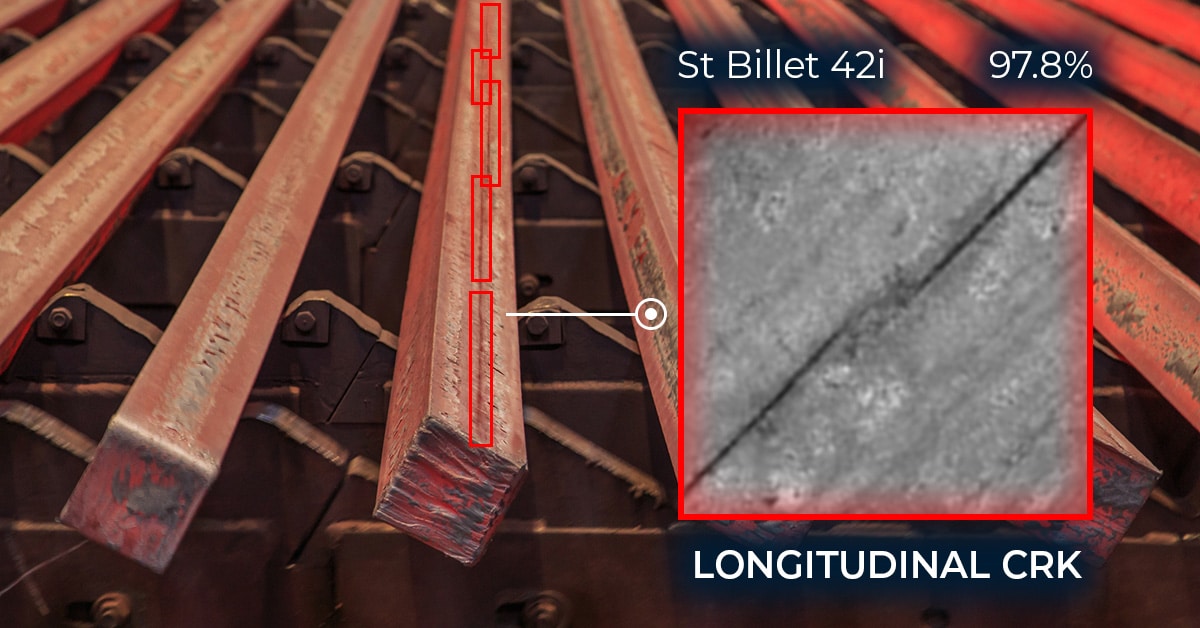
Rising raw material costs. Strained labor markets. Regulatory expectations. Steel and aluminum manufacturers today face more pressure than ever. Progress will depend on embracing new technologies and approaches. But what does innovation look like in an industry long defined by tradition?
The answer: smart manufacturing driven by AI-powered computer vision.
Matroid’s no-code computer vision (CV) platform helps manufacturers cut costs, become more efficient, and meet enhanced environmental regulations. It’s about building capability for the present and resilience for the future.
To explore how computer vision is already transforming operations across the industry, read our white paper: Computer Vision Drives Sustainable, Cost-Saving Innovation in Steel and Aluminum Manufacturing.
Rising Costs, Fewer Workers, Stricter Standards
Steel and aluminum are foundational to infrastructure, automotive, aerospace, and countless other sectors. But producing them comes at a cost, environmentally and financially. Steel production alone consumes nearly 35 exajoules of energy annually and contributes to roughly 10% of global CO₂ emissions.
With labor availability tightening and regulatory expectations increasing, the industry is under growing pressure to adapt. Many manufacturers find that advanced tools like AI and computer vision can drive new efficiencies and reduce risk.
AI-Powered Defect Detection That Works in Harsh Environments
Traditional inspection processes in metal manufacturing are slow, manual, and error-prone. Matroid’s AI-powered defect detection systems flip that model. Manufacturers can use high-precision computer vision to detect real-time flaws like cracks, dents, porosity, and casting voids. The technology performs reliably even in high-heat, high-speed environments where human inspection often falls short.
Whether it’s a weld bead that’s off by a few millimeters or a hairline surface crack in an aluminum sheet, AI can identify problems early and accurately. That means less rework, fewer production delays, and significantly lower material waste.
In one example, a major U.S. steel producer used Matroid’s platform to boost defect detection accuracy from 70% to over 98%, cutting $2 million in annual labor costs and dramatically reducing scrap.
Smarter Workflows, Safer Teams
Beyond defect detection, AI-driven computer vision supports a smarter, safer workforce. With an aging labor pool and increasing automation, manufacturers need ways to streamline operations and prioritize safety without adding headcount.
Matroid’s system identifies inefficient workflows, monitors task distribution, and even flags unsafe behaviors, like improper lifting or unauthorized entry into restricted zones.
One Matroid client increased compliance from under 25% to over 90% using existing video feeds and AI monitoring. Within a year, they reduced safety incidents to zero.
It’s not about replacing workers; it’s about empowering them with better tools and insights to improve both productivity and well-being.
Sustainability Meets ROI
Implementing environmentally conscious practices like electric arc furnaces or hydrogen-based steelmaking is a step in the right direction. Still, these innovations may come at too high a cost without operational efficiency.
This is where Matroid’s CV helps again by automating inspections, minimizing errors, and tracking material flow in real-time. Companies can dramatically reduce energy use, scrap rates, and downtime with better data and decision-making. Meeting compliance is only part of the equation; long-term value comes from aligning sustainability with operational efficiency.
Matroid’s platform can categorize and track scrap metal used in support of circular manufacturing, helping companies confidently incorporate recycled materials into their production lines. It’s a streamlined way to localize materials and build supply chain strength.
Plug-and-Play Integration for Maximum Impact
A defining strength of Matroid’s solution is its flexibility. The platform is camera-agnostic, deployable on cloud or edge, and integrates seamlessly with existing production hardware. No major overhaul. Just results.
Any facility can scale the solution from fabrication shops to massive industrial plants to match its needs. Whether you’re focused on safety, quality, sustainability, or all three, Matroid’s system delivers real-world impact without a steep learning curve.
Lead the Transformation
Steel and aluminum manufacturers are at a crossroads: adapt with advanced technologies or risk falling behind. No-code and built to scale, Matroid’s computer vision platform gives manufacturers a competitive edge. It drives higher quality, cuts costs, and accelerates the move toward more sustainable production.
Matroid is helping lead that change, making AI accessible and actionable for manufacturers of all sizes.
Download the full white paper to explore how computer vision is reshaping metal manufacturing – or book a personalized demo to see Matroid in action at your facility.
Building Custom Computer Vision Models with Matroid
Dive into the world of personalized computer vision models with Matroid's comprehensive guide – click to download today