AI-Powered Welding: How Computer Vision Solutions Drive Precision and Efficiency in Metal Manufacturing
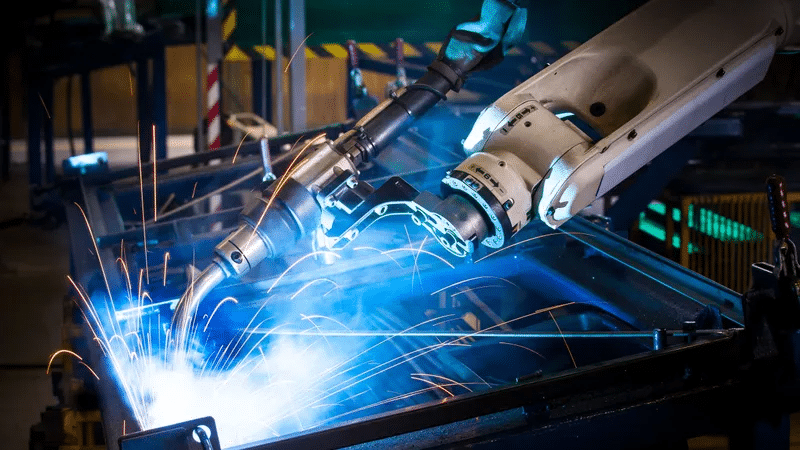
Jeff Zeller | November 20th, 2024
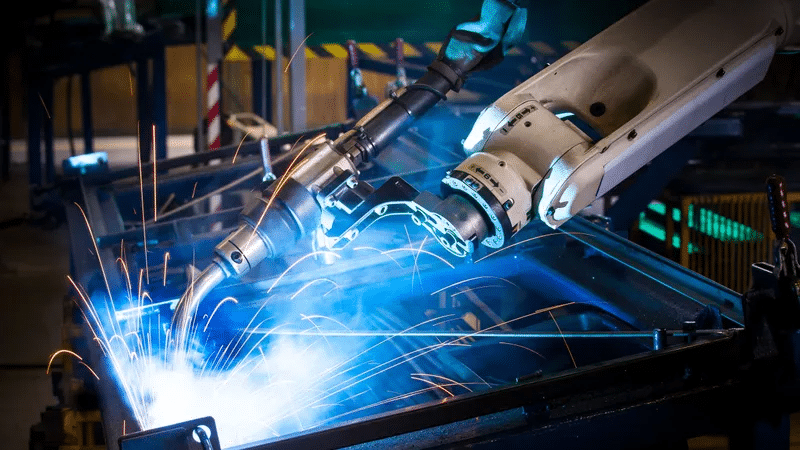
Discover how computer vision is solving quality challenges in metal manufacturing through enhanced defect detection, proactive process monitoring, and flexible integration solutions.
Guest Article from Deval Shah, Senior Machine Learning Engineer @ Wevolver
Automated welding is on the rise in manufacturing, significantly boosting production efficiency. However, manufacturers are discovering that even automated systems can drift from established standards over time, especially when working with new materials or products with complex designs.
As production lines become more sophisticated and quality standards more stringent, traditional inspection methods must be revised for modern manufacturing demands.
Matroid is transforming this landscape by democratizing computer vision technology, making advanced automated visual inspection accessible to industry professionals without coding expertise. Through its innovative platform, Matroid enables manufacturing teams to implement sophisticated defect detection and process monitoring solutions that can be deployed within minutes rather than months.
The impact is significant in welding applications, where Matroid’s computer vision technology can evaluate multiple quality parameters simultaneously – from porosity and spatter to burn-through – with the precision of a weld engineering expert.
This scalable approach to quality control is proving essential as manufacturers face mounting pressure to maintain precision while managing costs.
We will explore in detail how Matroid’s computer vision technology is changing the landscape of metal manufacturing, examining its technical capabilities, practical applications, and the tangible benefits it brings to production environments. For decision-makers, we’ll look at how this technology sets new standards in automated quality control and process optimization.
Industry Challenges and Opportunities in Metal Manufacturing
Current Challenges in Metal Manufacturing
The metal manufacturing industry faces unprecedented pressures, with many organizations’ quality control costs consuming 15-20% of annual sales revenue. Traditional manual inspection methods, while common, are increasingly inadequate for modern manufacturing demands, showing inconsistency rates increase due to operator fatigue and subjective assessments.
According to a US Census Bureau study, production facilities struggle with a critical shortage of skilled workers, with nearly one-fourth of the manufacturing workforce aged 55 or older. This demographic shift and early retirement trends post-pandemic have created significant gaps in quality control expertise and operational efficiency.
The Role of Automation and Computer Vision
Computer vision & AI technology is emerging as a transformative solution, capable of analyzing images and video from any imaging technology, spanning resolutions from low (VGA) to ultra-high (gigapixel) and across various spectra, including visible light, infrared, and x-ray. This enables the detection of the smallest and most challenging defects in manufacturing processes, enhancing quality control and operational efficiency.
Unlike traditional rule-based inspection systems, modern computer vision & AI solutions can detect and classify multiple defect types simultaneously, from surface imperfections to welding anomalies.
Automated inspection systems are valuable in welding applications, where they can evaluate multiple quality parameters – including porosity, spatter, burn-through, edge welds, and cold welds – with consistent precision.
Computer vision & AI address the skilled labor shortage and significantly improve inspection accuracy, with some implementations showing up to 10x improvement in defect detection compared to conventional methods, which leads to dramatic cost savings in cost per part and rework efforts and also improves production throughput. In parallel, the appeal for the next generation of labor to work with new cutting-edge technology, such as computer vision & AI, is bringing new levels of local talent to manufacturing companies.
Matroid’s Vision and Technological Focus
Founded in 2016 by Stanford professor and founding member of Databricks Reza Zadeh, Matroid has established itself as a leader in enterprise-level computer vision & AI software platform, backed by $33.5M in funding from prominent investors, including NEA, Energize Ventures, and Intel Capital.
The Matroid platform empowers domain experts from manufacturing to rapidly deploy and adapt custom detectors that can leverage camera systems’ imagery/ video types to detect and classify defects, monitor manual assembly operations, verify SOPs are followed, and provide continuous cycle-time analysis with unprecedented precision across various production environments.
Custom Detectors and Real-Time Monitoring
Matroid’s platform distinguishes itself through its no-code software to build and deploy detector systems end-to-end, allowing manufacturing teams to develop specialized detection models tailored to their needs through an intuitive point-and-click interface.
These vision detectors can simultaneously evaluate multiple quality parameters in metal processing applications – from weld porosity and spatter to surface defects and assembly errors – while maintaining consistent accuracy across varying conditions.
The platform’s camera-agnostic system integrates seamlessly with existing infrastructure, supporting everything from standard industrial cameras to specialized equipment like borescopes, microscopes, and X-ray systems.
Real-time alerts and analytics are delivered directly with production systems (PLCs, SCADA, MES, ERP, databases) and mobile devices. This enables immediate response to the right people and systems at the right time to detect anomalies and maintain digital traceability throughout manufacturing.
How Matroid’s Computer Vision Powers Welding Applications
Detecting Defects in Metal Manufacturing
Matroid’s computer vision enables quality control oversight across the entire metal manufacturing process. The system identifies structural defects at the casting stage, like cracks, porosity, cold flow, and hot tears.
Within the stamping processes, Matroid detectors are used to replace manual visual inspection by automating the inspection of stamped parts for tears and splits. This gives near real-time feedback to production engineers on how the presses are performing and gives insights into potential adjustments to prevent further defects.
In the final inspection, the platform performs comprehensive checks to ensure consistently high quality, effectively reducing returns and warranty claims.
Computer Vision in Welding
Matroid’s technology monitors operations such as spot welding, MIG welding, and continuous seam welding through real-time monitoring and instant defect detection. The system evaluates multiple quality parameters simultaneously, identifying common issues like porosity, spatter, cold welds, edge welds, and burn-through, just as a weld engineering expert would.
The platform’s deep learning capabilities enable it to detect defects as a person could through visual media (images/video). The solutions are designed for rugged & dynamic manufacturing environments.
Root Cause Analysis and Real-Time Adjustments
Matroid’s solution provides detailed defect classification and analysis through its integrated system. The system immediately alerts operators when issues are detected through direct integration with production systems, QMS, and mobile devices. Production teams can take corrective action when they have near real-time classification information and analytics; for example, when burn-through is detected on welds, the welding engineer can make more effective adjustments to robotic welding systems faster. This reduces rework and defect risks and improves production throughput.
The platform operates 24/7, providing continuous monitoring and real-time insights into production operations. Through its historical data analysis capabilities, manufacturing teams can capture actionable insights and implement zero-defect initiatives.
Real-World Applications and Benefits
Traditional Methods vs. Computer Vision & AI for Welding
Traditional welding inspection methods, relying on manual or basic automated systems, provide only binary pass/fail results. These systems need help to meet modern manufacturing demands, where quality teams need detailed defect analysis and real-time process adjustments.
Manual inspections introduce delays between defect occurrence and detection, while inspector fatigue and varying experience levels lead to inconsistent results. Computer vision & AI solutions powered by deep learning technology transform this landscape by enabling real-time identification and classification of specific weld defects.
Matroid’s system automatically detects and categorizes issues such as porosity, burn-through, and spatter, immediately notifying weld engineers for rapid response. This immediate feedback loop allows manufacturing teams to identify root causes and implement real-time process adjustments quickly.
The deployment of edge or on-premises installations ensures minimal latency for real-time monitoring while maintaining data security. This approach enables manufacturing teams to shift from reactive quality control to proactive process optimization.
Through consistent quality assessment and automated defect classification, companies can reduce inspection time, minimize waste, and improve overall welding quality. The system’s integration with existing production processes creates a seamless transition from traditional inspection methods to advanced computer vision & AI solutions.
The Deployment of Matroid’s Solution
Easy Integration and Deployment
Matroid’s computer vision & AI platform integrates seamlessly with existing manufacturing infrastructure through multiple deployment options. The system can be implemented as downloadable software for on-premises installation or as a Cloud software service, allowing manufacturers to choose the deployment method that best suits their operational needs.
This flexibility enables manufacturing teams to maintain data security while leveraging advanced detection capabilities. Matroid’s platform makes integration into various control systems, MES, QMS, ERP, and databases easy so that production can work with real-time data and has enhanced product traceability.
Compatibility with Multiple Camera Technologies
The platform’s camera-agnostic approach sets it apart in the manufacturing sector. Matroid works with existing and new vision systems, supporting any image-or-video-based camera regardless of resolution (VGA – giga-pixel) or spectra (visible, infrared, X-ray, etc.).
This allows manufacturers to reuse their existing machine vision cameras and use the right imaging technology for the application at hand while maintaining the ability to detect visual defects. The system connects effortlessly with industrial cameras, supporting continuous 24/7 monitoring and real-time insights into manufacturing processes.
Future of Welding with Computer Vision & AI
Integrating computer vision technology in welding operations represents a significant leap forward in manufacturing quality control. Matroid’s platform transforms traditional inspection methods by enabling real-time defect detection and detailed classification, which enables immediate process adjustments.
By combining deep learning capabilities with enterprise-grade deployment options, manufacturers can achieve consistent quality while reducing operational costs. The platform’s ability to empower domain experts in manufacturing, work with existing infrastructure, and support multiple camera technologies makes it a practical solution for facilities of all sizes.
Ready to make your welding operations efficient and reliable with advanced computer vision?
Discover how Matroid’s platform can enhance your quality control processes and drive real-time improvements at matroid.com.
References
- https://info.matroid.com/visual-inspection-computer-vision-software
- https://www.dayjob.com.au/metal-fabrication-challenges-with-sustainability/
- https://www.matroid.com/automated-visual-anomoly-detection/
- https://www.qualitymag.com/articles/98221-advances-in-computer-vision-offer-a-clearer-path-to-reliable-quality-control
- https://www.weboccult.com/blog/computer-vision-for-quality-control-in-manufacturing-a-comprehensive-guide
- https://cloud.google.com/blog/products/ai-machine-learning/improve-manufacturing-quality-control-with-visual-inspection-ai
- https://www.matroid.com/automated-visual-anomoly-detection/
- https://www.qualitymag.com/articles/98221-advances-in-computer-vision-offer-a-clearer-path-to-reliable-quality-control
Building Custom Computer Vision Models with Matroid
Dive into the world of personalized computer vision models with Matroid's comprehensive guide – click to download today